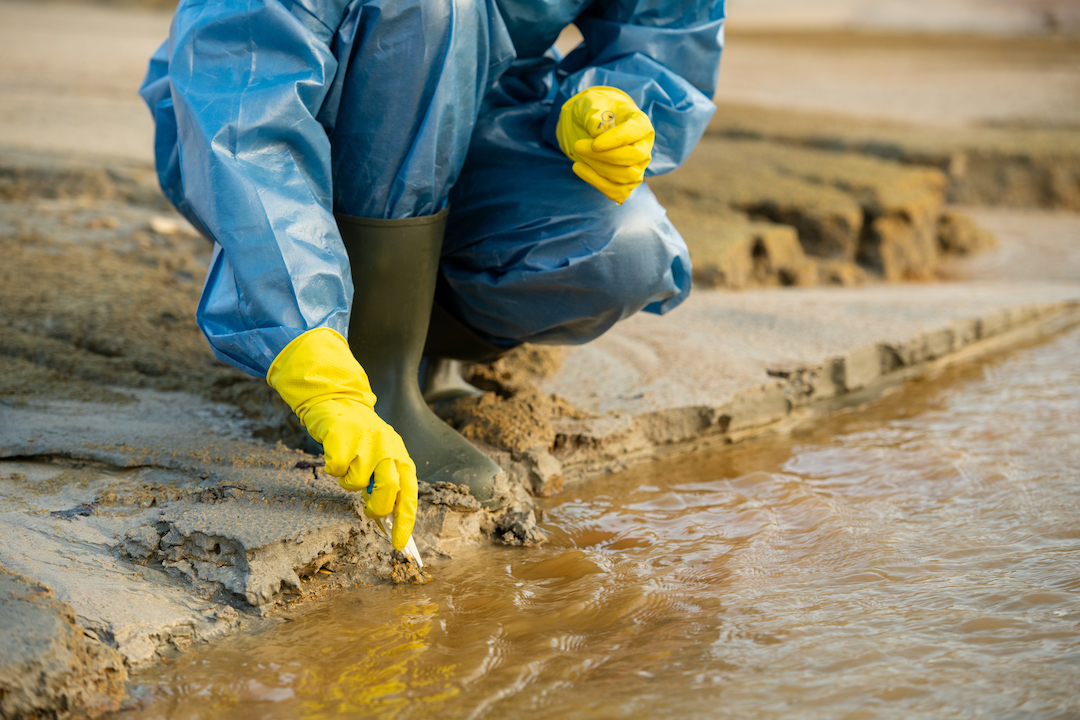
How to Reduce Sampling Costs in Accordance with NDPDES Wastewater Regulations
The National Pollutant Discharge Elimination System, or NPDES, has regulations for facilities that discharge pollutants into waters in the United States. It regularly evaluates each entity's compliance efforts to determine if they meet effluent limitations and reporting requirements for a permit.
Compliance is an added expense for every company, and leaders must find ways to keep wastewater sampling costs reasonable without risking a permit violation. There are several ways to evaluate sampling costs to see if there are any opportunities to save money. To better understand them, it helps to know and identify the specific factors that affect an individual company.
Understanding Factors That Affect Sampling
The frequency, location and methods can all affect cost. Because of ecological and operational differences that exist among facilities, specific details in permits can vary. When permit writers initially create the permits, they must consider all those factors, and they must consider them carefully in ongoing monitoring to ensure accurate compliance determinations.[1] These are some examples of the specific factors that can affect sampling frequency, method and location:
- Types of pollutants that are discharged.
- Variability of waste stream and processes.
- Sample location access.
- Effluent limitations.
- Pollutant load or flow effect on receiving water.
- Discharged pollutant characteristics.
- Frequency of discharge.
- Permit holder's history of compliance.
The potential ways to reduce costs may depend partially on several of these factors. If there is an existing inefficiency that can be corrected, costs may be reduced. Also, as operations or processes change, sampling requirements may change.[1]
Potential Cost Reductions for Wastewater Sampling
A careful analysis or audit of current processes may reveal one or more ways to potentially reduce sampling costs in relation to NPDES requirements. When doing this, it is also important to keep all permit requirements in mind.
In-House Participation
Some facilities may save money on sampling costs by either utilizing or eliminating in-house processes to conduct sampling. While in-house sampling may be feasible for some larger organizations, it may not be an ideal consideration for others. For example, one study of cost comparisons for sampling showed that maintaining in-house testing capabilities in areas where there were more limited sampling requirements was not a cost-effective choice.[2] To determine if in-house sampling is helpful for a larger facility, the cost of the staff and the entire sampling workload must be considered in comparison with the cost of using an outside agency, paying lab fees and paying other expenses to meet all sampling requirements.
Updating Monitoring Requirements
In many cases, there are facilities that develop and maintain a positive compliance record for specific NPDES parameters, but they are still required to continue frequent sampling and monitoring.[3] If a facility has a good record of compliance, and if frequent monitoring is no longer necessary, it saves time and money for facilities. NPDES may periodically remove frequent sampling requirements when they are no longer necessary. Since monitoring requirements are typically specific to a particular site or facility, it is important to report any facility changes that may impact those monitoring requirements as quickly as possible. Also, eliminating the associated unnecessary or irrelevant reports can potentially reduce costs for both evaluators and facilities.[3] Because of these factors, whenever permit conditions are refined by NPDES, it is important to analyze the sampling processes to look for change opportunities that may be financially beneficial.
Full Compliance
Sampling frequency and difficulty may both be greater when facilities do not meet all requirements. It is important to comply with NPDES requirements, but it is also important to stay in compliance with any other regulatory sampling requirements for testing programs if they exist or apply to the facility. In some instances, some of the requirements of such programs may overlap with those of the NPDES.[3] The water sampling points for NPDES are typically chosen based on ease of access to the water stream. If there are any potential overlaps or similarities in programs, it is important to ensure that full compliance with NPDES rules is maintained. No requirements should be skipped or overlooked because of a similar requirement with another entity. When a permit holder establishes and maintains a good history of compliance with permit requirements, there is less risk of having to meet stricter sampling and reporting requirements.[4]
Considerations in Hiring an Environmental Firm for Sampling and Compliance
Today, many facilities work with environmental firms that provide sampling services and compliance assistance. As noted in a previous section, handling sampling and related services may consume too much time and money for some facilities to maintain as in-house tasks. In addition to possibly saving money on services, working with an experienced environmental firm may also help reduce potential mistakes that could lead to higher costs. For example, not meeting a permit requirement and having to maintain frequent sampling as a result could lead to unnecessary costs. To make a sound financial choice in hiring, there are two important factors to consider in working with an environmental firm for wastewater sampling and related services.
Knowledge
A firm will typically educate clients on important sampling options and their costs, and these recommendations can be confirmed by reviewing information from the EPA. For example, composite sampling may be used in some applications to save money since it can help reduce laboratory costs by compositing multiple analyses into one.[5] Recent research has also reduced some of the limitations it had in the past. Working with a firm can help a facility better understand sampling options, compliance and ways to save on costs. Whether the facility plans to continue working with the firm or develop in-house processes in the future, starting with a knowledgeable firm is important.
Services
Reliable firms should offer a variety of services, and they should customize them for each facility. For example, the sampling and services that the firm provides should match what the facility's permit requires. Firms typically perform grab samples and composite samples, including both time-weighted and flow-weighted composite samples. Also, firms should preserve samples in accordance with regulations outlined in 40 CFR Part 136.[6] Today, many firms also handle important reporting and paperwork, including chain of custody documentation and more. They may also coordinate all required lab analyses for samples. Testing methods and devices must meet regulatory requirements, and firms typically maintain an updated inventory of all important equipment. They use flow meters, automatic samplers and other field instruments that help permit holders stay in compliance with the terms of their permits. Also, firms typically have their own in-house quality control measures to help prevent errors.
Today, there are firms that work with facility managers or leaders who have limited resources and do not have time to learn all the complexities of NPDES permit compliance requirements. For such clients, firms can usually help by analyzing the facility's permit terms. Based on the wastewater discharge permit terms that are specific to that facility, a firm can determine how to help save money by choosing the right sampling methods and complying with all wastewater sampling requirements. Firms also stay current with federal, state, and local sample collection requirements, and they typically have OSHA-certified technicians who collect samples.
At Magical Chemicals, we are working to solve these problems. To work with us visit our contact page.